Selecting Stainless Steel Grades For Your Retaining Ring or Wave Spring
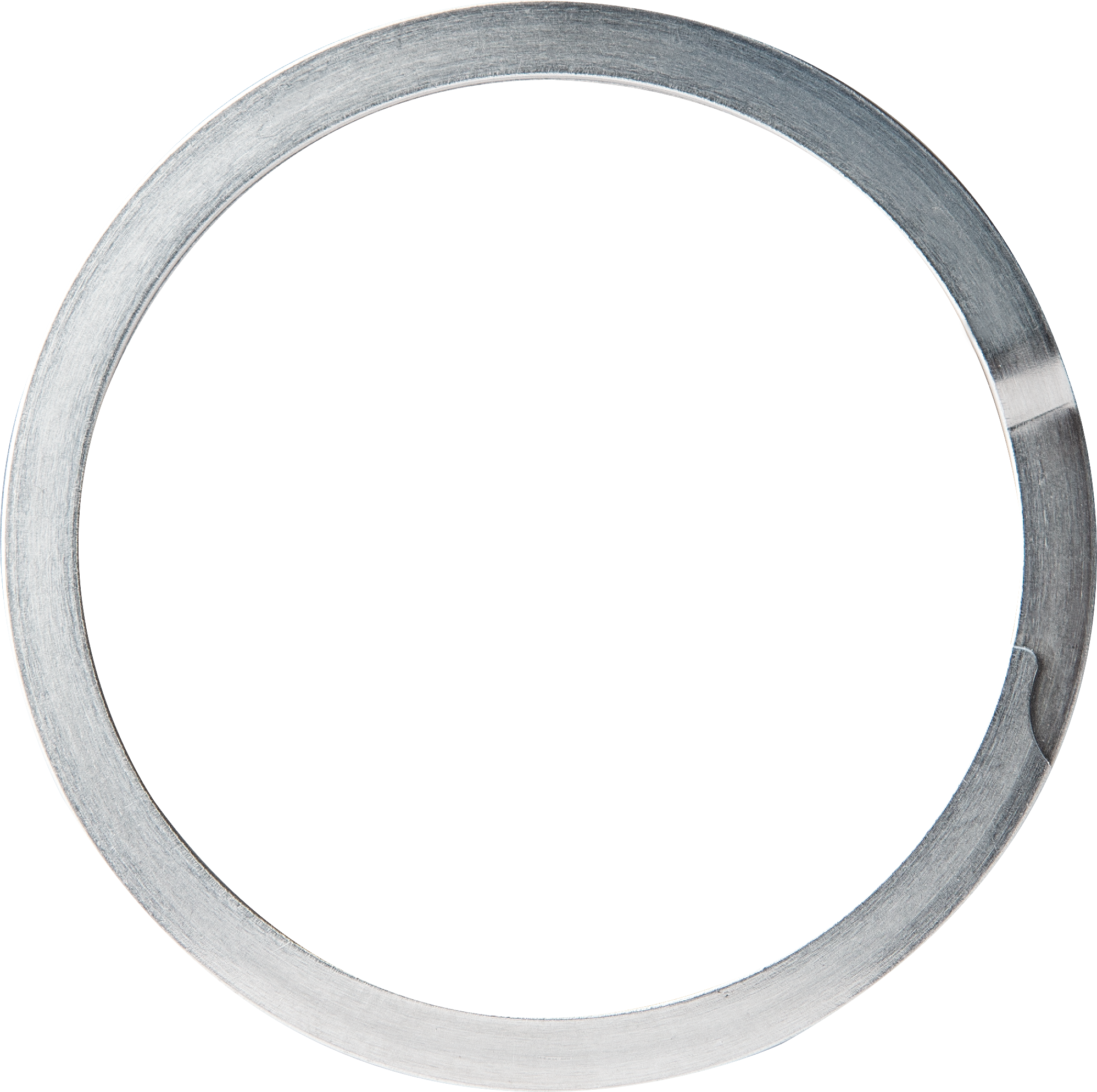
What are the main factors to consider when selecting a grade of stainless steel?
When selecting a grade of stainless steel for your retaining ring or wave spring, it is most important to assess the customer needs and consider what the part will be subjected to. The main factors for consideration are:
- Budget – Stainless steel is typically a more expensive option than our standard Carbon steel. The grade of Stainless steel you select will also result in differing prices.
- Protection – It is important to consider what the ring will be subjected to once in the application and therefore what level of protection the part will require. For example, will the part be exposed to a saltwater environment and therefore require corrosion resistance?
- Operational temperatures – In certain applications like jet engines and gas turbines, metals are subjected to extreme temperatures. Their ability to maintain strength can lessen and their properties change. High strength is essential to retain the shape of the part in a groove, or the shape of the spring.
- Magnetism – certain applications such as MRI, or directional drilling machines, may require the part to have no magnetic properties. Stainless steels are typically non-magnetic, but due to certain manufacturing processes the parts can inherit residual magnetism, so be sure to consult with a Rotor Clip engineer before final purchase.
Why should I choose stainless steel over standard carbon steel?
Stainless steel is generally used for applications where a standard carbon steel part would not be protected. When the retaining ring or wave spring is exposed to destructive factors such as grease, saltwater, or extreme temperatures, that carbon steel would not be able to withstand. Although it may incur a slightly higher price, stainless steel has the ability to maintain higher strength to higher temperatures and has better corrosion resistance, making it a superior choice in many applications.
If stainless steel is more expensive, why not just plate/coat a carbon steel part?
When price and budget is the most important factor in your material selection, plating a carbon steel part may still be a good option. We do not, however, recommended this as an option for applications where the plating could be damaged, chipped or compromised. Stainless steel has a passive layer which heals itself, meaning it remains corrosion resistant. If a plated part is damaged, an operational issue may arise well before rust becomes visible which could result in fracture, snap or even failure of the part. Plating can also cause hydrogen embrittlement, which is when hydrogen enters the part material, making it brittle.
Weakening of the parts can be catastrophic in applications, particularly those with lots of movement that use a wave spring. Any of these previously mentioned factors could cause complete application failure and machine down time. Overall, by selecting a grade of stainless steel for specific applications and environments which require it, there is much less margin for error.
So, what grades of stainless steel are available at Rotor Clip and what are their properties and benefits?
PH 15-7 Mo (Rotor Clip Part Code SS)
- Extra strength, corrosion-resistant steel.
- Capable of preventing atmospheric oxidation at temperatures up to 900◦F (482◦C).
- Primarily used for stamped parts.
- Minimal distortion due to its heat-treating process.
- High creep strength.
17-7 PH (Rotor Clip Part Code SS)
- Maximum operating temperature – 650◦F (343◦C).
- Primarily used for coiled product and wave springs.
- This is coiled in cold worked conditions to a certain tensile strength.
- Precipitation hardened which raises properties to more than 302/316
DIN 1.4310 (Rotor Clip Part Code SK) n.b. AISI 301 but does cross over to AISI 302, so DIN ID preferred.
- Similar properties to AISI 302 (the standard stainless grade used for snap rings).
- Often a much cheaper alternative to any requests for zinc plated carbon snap rings.
AISI 302 (Rotor Clip Part Code SJ)
- The starting point, general purpose stainless steel.
- Protects from typical environments with no major attacking factors.
- Maximum operating temperature – 650◦F (343◦C).
- Cold Worked & sometimes stress relieved.
AISI 316 (Rotor Clip Part Code SU)
- Next step up from 302.
- Good for environments requiring lots of cleaning e.g., medical and food processing or those exposed to saltwater environments such as naval.
- Heat resistant but with superior corrosion resistance to other grades.
- Maximum operating temperature – 650◦F (343◦C).
- Will be higher cost due to alloys used.
- Cold Worked & sometimes stress relieved.
Type 420 - DIN 1.4122 (Rotor Clip Part Code SG)
- A less expensive alternative to 15-7.
- Less corrosion protection than 15-7.
A286 (Rotor Clip Part Code SY)
- High specification stainless steel, capable of operating in temperatures of up to 1,000°F (538◦C).
- Typical aerospace grade when in close proximity to jet or exposed assemblies.
For requirements other than these, next options will be super alloys such and other materials such as Beryllium Copper & Phosphor Bronze. These material grades often incur more expense.
For more on materials and finishes, contact info@rotorclip.com