Selecting The Right Wave Spring End-Type
.png)
Traditional coil springs are widely used throughout a variety of applications across nearly every industry. The typical end configuration for coil springs is where you have a helix, and the last turn is bent down, touching the second to last turn and ground to form a shim.
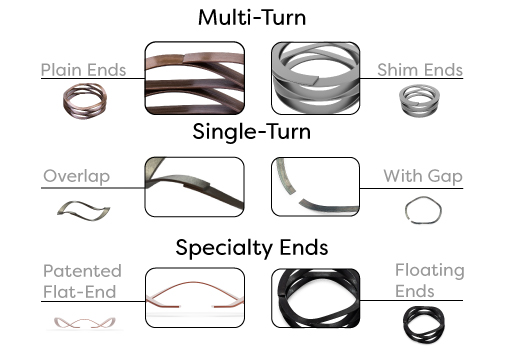
Rotor Clip manufactures the largest range of wave springs in the market, with the ability to manufacture springs from 3 mm to 635 mm. Wave springs offer space savings in an axial direction, in which 50% of the operating height can be reduced. Wave springs produce loads in shorter spaces by distributing the loads over the waves themselves from bending, opposed to torsion. When specifying wave springs, there are many features that can be modified to suit individual application requirements. Whether you need a custom or if a standard configuration works, when it comes to coiling, modifications and customizations are often simple, as it’s just an adjustment and no special tooling is needed.
With multi-turn wave springs, customers often think they need a shim ended part based on conventional coil spring designs. However, Rotor Clip engineers can help assess the right end-type for wave springs based on your application requirements. Here are the following end-type configurations offered for both single-turn and multi-turn wave springs:
Multi-Turn Wave Springs
Plain Ends
Plain ends are the standard and generally most commonly spec’d end-type for multi-turn wave springs, in which the end stops at the next peak.
Shim Ends
Shim-ends are a configuration with two extra flat turns/layers of material to further support even loading on the top and bottom surface. Although, wave springs typically sit flat, in certain cases a shim-ended part would be beneficial if there’s an uneven surface that the spring is sitting upon. The shim end will bridge the unevenness in the application. For example, a case for utilizing a shim end is when waves can potentially fall into a trough, a hole or slot, that is an uneven mating surface.
Another reason to utilize a shim-end for a wave spring is for soft material (such as plastics, rubbers, soft metals, etc.) that the spring is mating with. You add a shim if each wave is pushing on something soft, while there’s a high load for distributing it as much as you can around the circumference. As a result, the wave spring is pushing on the shim, which is uniformly distributed over the soft material.
Shim ends can occasionally have alternative design functions that allow them to positively impact application performance. On occasions, multiple shims have even been added to help affix the spring to the mating component by winding the ends into a groove.
Single-Turn Wave Springs
Single turn wave springs, often specified for taking up tolerances or providing a preload in an application are available in assorted configurations. There are couple of options for selecting the appropriate end-type for single-turn wave springs. The main discussion points for whether your application calls for gap or overlap ends is based on the method of packaging, assembly, and design aspects of the solid height.
Gap
These types of ends have a physical gap. We are able to control the distance of the gap, as there may be components that need to clear that gap. Rotor Clip engineers have even patented a type of single-turn wave spring with flat ends. Our patented flat-ends protect bearings by eliminating sharp, damaging corners from the spring ends, instead flattening them so they rest smoothly against the mating assembly. It’s another reason why designers are increasingly discovering flat wire wave springs as an attractive option for spring-loaded applications.
Overlap
An overlap single-turn wave spring has an end configuration in which the ends come together with one end “overlapping” the other. The result of this end-type offers no digging while mating with the surface. Another benefit of having no open gap, you eliminate parts being tangled in a bulk packaging arrangement.
Specialty End-types
Floating Ends
Typically, with multi-turn wave springs the end comes down and rests on a peak of the turn below it. When the wave spring is compressed, that end is sitting on the mating surface, which could be an area that can allow scratching. This is especially the case if the wire thickness is very thick and promotes scratching in that concentrated area. For floating ends we’ll cut the end back a little bit, so the end is not resting on the peak. Like the name implies, the end is floating and when compressed the end curls down into the part itself. This type of end configuration greatly mitigates any ability to scratch the mating surface.
Conclusion
Rotor Clip engineers the right part, for the right application, whether its standard or custom. Providing Application Driven Solutionsᵀᴹ, we have the extensive experience designing products into applications across nearly every industry. Rotor Clip provides on-demand engineering support services designed around your needs! Whether you have a specific question about your application requirement or require general product training, we’ll deliver engineering support directly to you in the manner you choose - live web conferencing, face-to-face at your location or via phone or email. Need assistance on your selecting the right wave spring and end-type contact an engineer today.